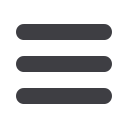
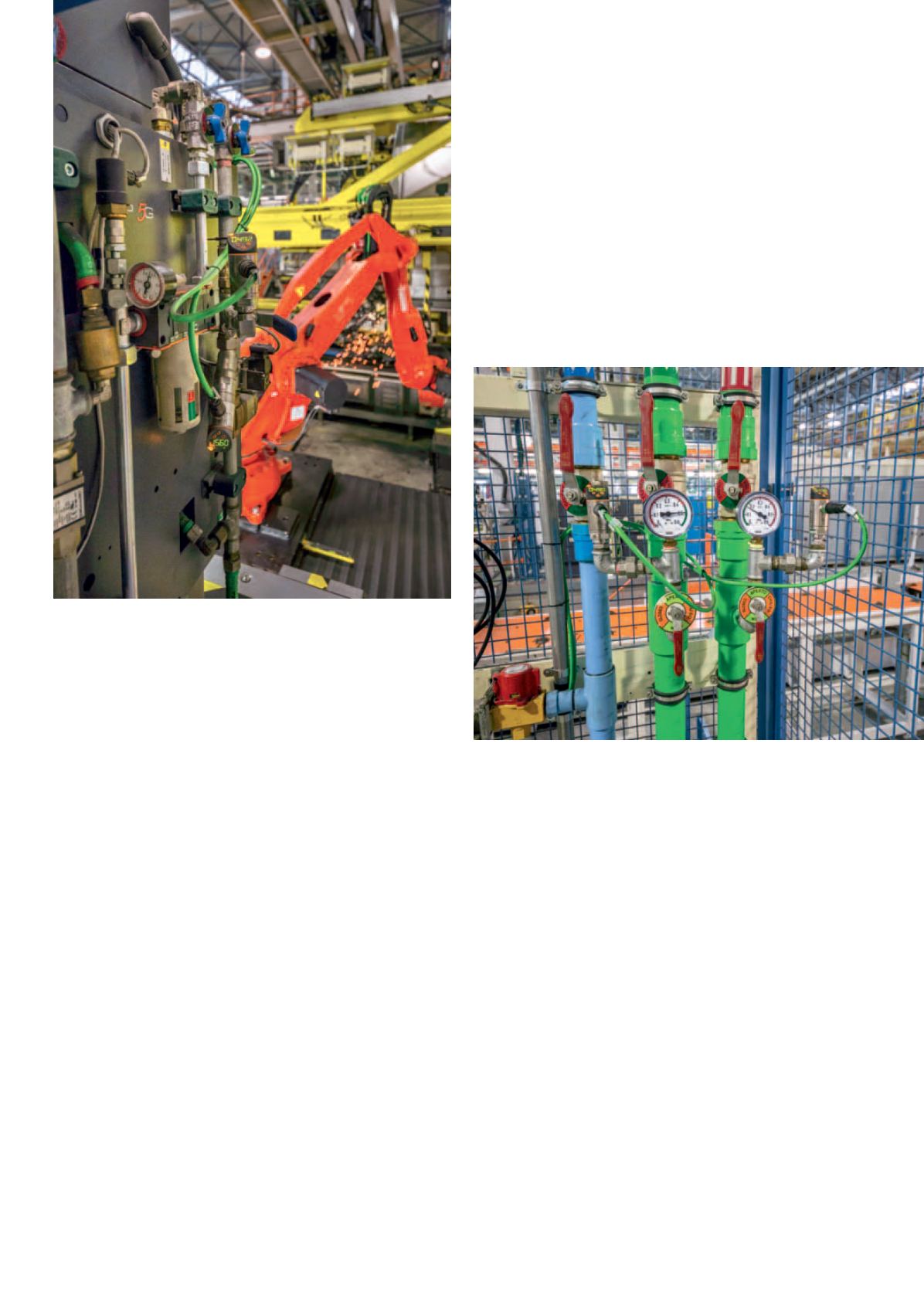
MAGGIO 2017
FIELDBUS & NETWORKS
41
detta ‘a ciclo’ a una manutenzione ‘a condizione’, con l’obiettivo di
migliorare l’efficienza produttiva contenendo al contempo i costi.
La soluzione chiavi in mano di ifm
Da tempo partner di Iveco e del Gruppo CNH Industrial, ifm electronic
ha da subito adottato un approccio globale nei confronti di questo
progetto, proponendosi al cliente come fornitore chiavi in mano di un
intero sistema di manutenzione predittiva e monitoraggio energetico,
comprensivo di sensoristica, software, server, installazione elettrica,
meccanica e collaudo.
La strategia adottata da ifm electronic per il revamping della linea ha
condotto all’implementazione di una soluzione per la manutenzione
predittiva e il monitoraggio delle energie, affiancando alle tecnologie
esistenti un sistema parallelo composto da sensori intelligenti, gate-
way e software di visualizzazione e analisi dati. Il sistema web based
permette la gestione tempestiva della manutenzione, il contenimento
dei consumi energetici e il conseguente miglioramento dell’efficienza
produttiva.
Solo dopo un’attenta analisi dei punti critici maggiormente soggetti a
usura meccanica sulla linea di lastratura, i cosiddetti ‘stressor’ (agenti
stressanti), si è passati a decidere quale strumentazione utilizzare per
prevenire guasti improvvisi e conseguenti fermi della linea.
Quali sensori per quali esigenze?
La molteplicità di componenti ed elementi da monitorare ha richie-
sto l’installazione di una gamma diversificata di sensori di processo
e di analisi vibrazionale. Innanzitutto, sulle parti soggette a usura
meccanica è stato implementato un sistema di analisi vibrazionale
basato su accelerometri Mems ifm VSA001 collegati a centraline di
diagnosi ifm VSE100. Queste ultime hanno il compito di elaborare il
segnale proveniente dai Mems effettuando trasformate di Fourier e
analisi nel dominio del tempo per poi trasmettere i risultati, mediante
connessione Ethernet, al software di supervisione ifm Linerecorder
SmartObserver. Parallelamente, si è passati ad analizzare l’attività
dei robot antropomorfi per garantirne un’elevata performance, per
cui le pinze di saldatura devono poter contare sulla presenza ade-
guata e calibrata del liquido di refrigerazione. Il rilevamento dei flussi
di questo liquido viene garantito dai sensori meccatronici ifm della
serie SBY che, oltre a trasmettere la portata istantanea, comunicano
la temperatura tramite protocollo IO-Link. Grazie al display bicolore
i sensori consentono una visualizzazione chiara e immediata dello
stato, anche a bordo macchina. Per il controllo della portata generale
del liquido di refrigerazione che rifornisce l’intera linea sono invece
stati scelti i sensori con tecnologia magneto-induttiva della serie SM.
Essi sono in grado di trasmettere, oltre alla portata istantanea sia
sul flusso di mandata sia sul flusso di ritorno, anche la quantità di
liquido consumato e la relativa temperatura. L’eventuale registrazione
di una differenza tra i due flussimetri SM permette di identificare im-
mediatamente una probabile perdita, un intasamento dei filtri o un
malfunzionamento delle pompe, consentendo al sistema di avvisare
automaticamente la manutenzione.
Per quanto riguarda la pressione di impianto generale e a bordo robot,
sono installati dei sensori di pressione intelligenti ifm della serie PN
in grado di trasmettere il segnale tramite protocollo IO-Link. Grazie al
display bicolore anche questi sensori consentono la visualizzazione
immediata dello stato anche a bordo macchina.
Oltre al rilevamento di tutti quei valori necessari alla definizione dello
stato macchina e alla conseguente implementazione di una manuten-
zione predittiva, su questa linea si vogliono misurare i principali vettori
energetici, al fine di contenere eventuali sprechi. Questo è possibile
grazie alla serie Metris di ifm per il monitoraggio dell’aria compressa
e ai flussimetri serie SM che controllano il flusso principale di andata
e ritorno del liquido di refrigerazione. Due flussimetri massico-termici
ifm della serie SD controllano costantemente la portata istantanea e
i consumi di aria compressa, in modo da intervenire a riparare tem-
pestivamente eventuali perdite ed evitare costosi sprechi energetici
sull’intera linea. Oltre a comunicare la portata istantanea, i sensori
SD trasmettono la quantità di aria compressa consumata e la tempe-
ratura tramite protocollo IO-Link.
I sensori SB e PN controllano la portata e la pressione del liquido di
refrigerazione
%
"& À