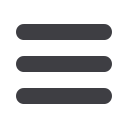
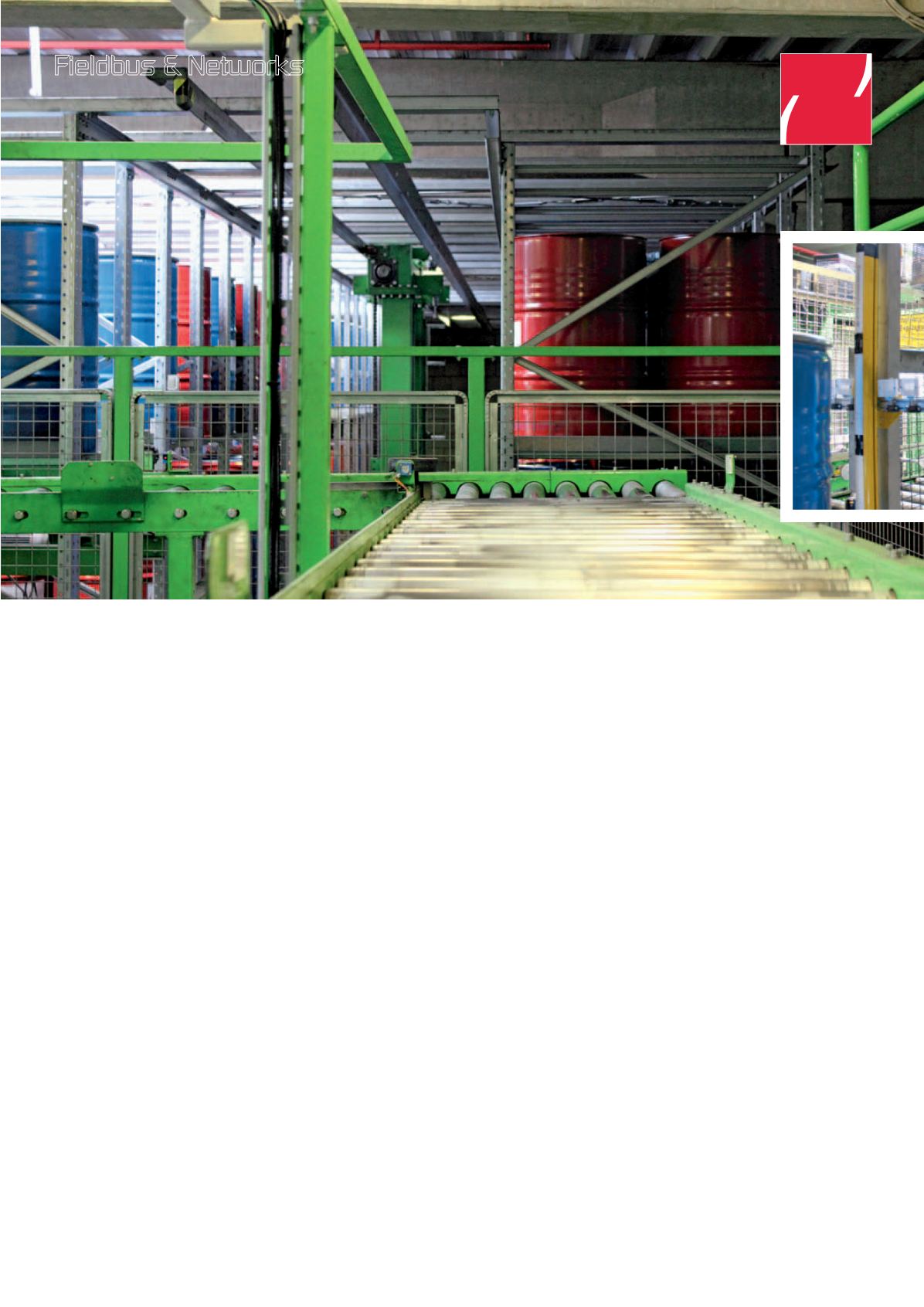
MAGGIO 2017
FIELDBUS & NETWORKS
36
DARE VALORE ALL’IMPIANTO
GRAZIE AL SISTEMA DI CABLAGGIO
INTELLIGENTE DI EATON, BASF HA
MINIMIZZATO I TEMPI DI INATTIVITÀ
NELLA PRODUZIONE DELLA PLASTICA
di
Carlo Lodari
I
l sistema di gestione dell’impianto Basf di Lemförde è un elemento
cruciale nella catena di processi che permette il trasporto dei barili
all’interno dell’impianto. Dopo 25 anni il sistema è stato ammoder-
nato utilizzando SmartWire-DT che, in collaborazione con i salva-
motori elettronici PKE Eaton, permette di misurare con semplicità la
potenza di ogni singolo drive. Nel caso in cui venissero rilevati valori molto
diversi da quelli attesi, i drive interessati possono essere disattivati in
modo controllato prima che il salvamotore entri in funzione, consentendo
così di implementare una manutenzione di tipo predittivo.
Il problema: aggiornamento
dell’automazione
Il poliuretano (PU) è uno dei polimeri più comunemente utilizzati al mondo;
la miriade di applicazioni per i quali viene impiegato, ovvero rivestimenti,
fibre, stampati ed elastomeri, ne dimostrano la versatilità. Questo ma-
teriale fornisce l’ammortizzazione ottimale nelle scarpe sportive, serve
come guarnizione nelle automobili, isola cavi e riduce il rumore attra-
verso i muri e i tetti degli edifici. Azienda nota in Europa per l’utilizzo di
questa tecnologia è Basf Polyurethanes GmbH, fondata nel 1962 e con
Dossier
Fieldbus & Networks
sede a Lemförde, vicino a Osnabrück, in Germania. In questo stabilimento
più di 1.500 impiegati generano vendite per oltre 2 miliardi di euro. Una
parte fondamentale dell’impianto è il sistema di trasporto dei barili: esso
trasporta barili da 200 litri pieni di materie prime o prodotti finiti dai re-
parti di produzione ai magazzini e viceversa. “Se il sistema di trasporto
non funziona perfettamente, il processo produttivo può andare incontro
a diversi problemi” afferma Claus Buhrmester, appartenente al team di
manutenzione.
Dopo 25 anni di funzionamento il sistema di trasporto dei barili non era
in grado di soddisfare i requisiti moderni. Thomas Büch, facente parte del
team di ingegneri di Lemförde, spiega: “L’impianto era controllato da tre
PLC che dovevano essere sostituiti, dal momento che i ricambi per questi
non venivano più prodotti. I livelli di sicurezza non erano i più aggiornati
e non avevamo a disposizione una chiara panoramica del funzionamento
dell’impianto. Non era inoltre possibile un intervento manuale per risol-
vere i casi di guasto”. Nell’ambito del progetto di ammodernamento si è
deciso di rivedere la tecnologia di automazione adottata. Nel corso di tale
processo, un totale di 50 motori trifase dovevano comunque rimanere in
funzione all’interno dell’impianto.
La soluzione: misura della potenza
su ogni drive
Nell’ambito del processo di modernizzazione, il sistema di trasporto dei
barili, che consisteva di tre linee controllate singolarmente, è statomodifi-
cato inmodo da essere controllato da un PLC. “Questo semplifica la strut-
tura dell’architettura di automazione e il raggruppamento dei tre quadri
di controllo in uno solo ci permette di risparmiare spazio prezioso” spiega