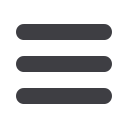
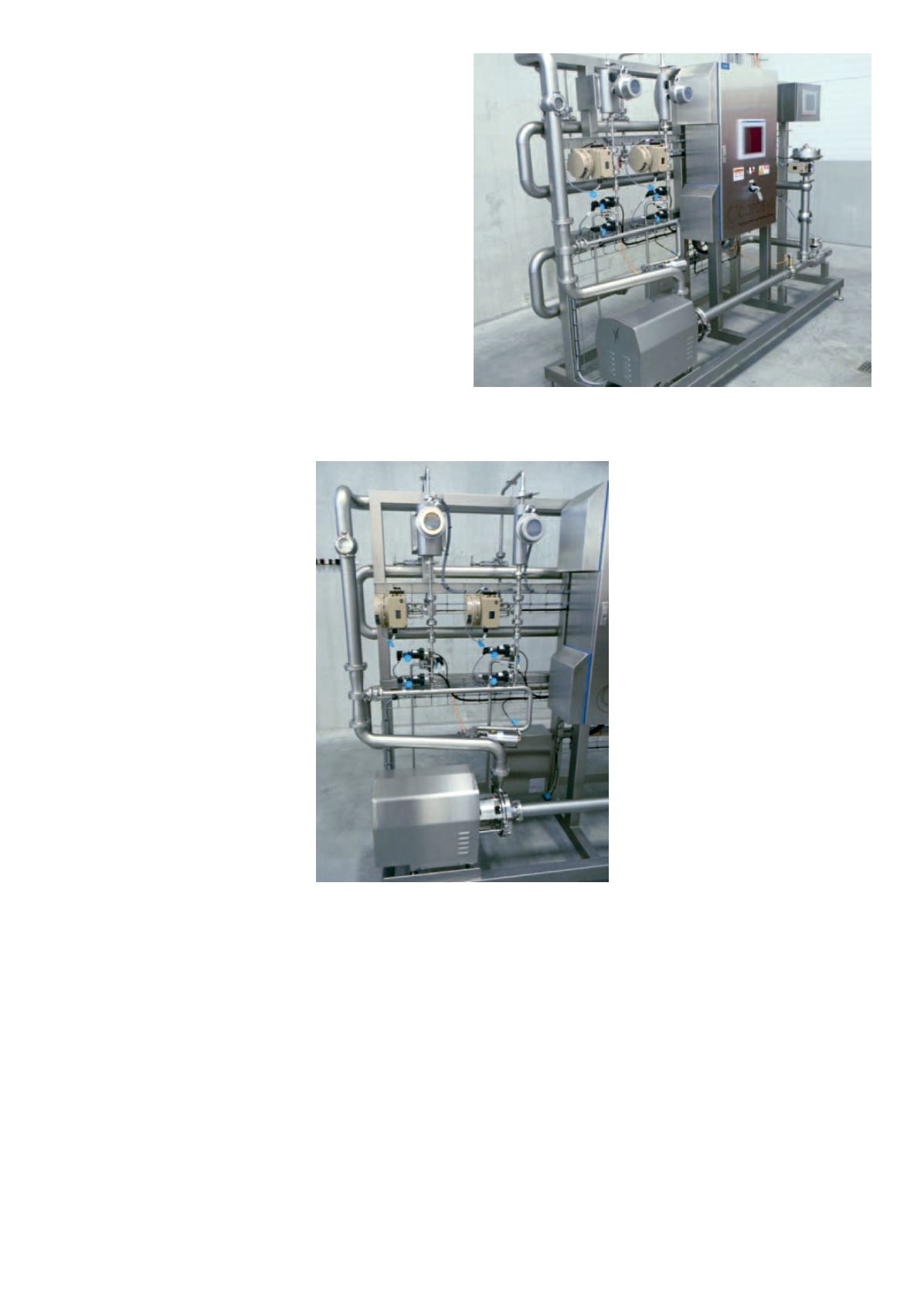
MAGGIO 2017
FIELDBUS & NETWORKS
35
Durante il funzionamento, la CO
2
viene iniettata nella birra tramite un
iniettore di gas GDI sviluppato da Corosys. L’iniettore di gas divide la CO
2
in bolle molto piccole per garantire che si dissolva in tempi molto rapidi.
La dispersione omogenea e l’assenza di bolle di gas possono essere mo-
nitorati tramite una spia posta alla fine del percorso di dissoluzione e il
contenuto di CO
2
viene continuamente controllato. Il set point specifico
di prodotto viene confrontato con il valore di processo e il flusso di CO
2
viene di conseguenza regolato tramite un algoritmo di controllo. La valvola
di controllo, che si trova alla fine del percorso di dissoluzione, mantiene
costante la pressione nel sistema, anche se il flusso è instabile. “Alla
fine, misuriamo il contenuto di CO
2
con un sistema di campionamento”
spiega Feider, che prosegue: “CompactLogix PAC viene utilizzato per
calcolare i livelli, utilizzando algoritmi avanzati e quindi regolare il flusso
per realizzare un mix ottimale. Il PAC controlla ingresso e uscita, in modo
che i livelli non debbano essere regolati in modo retrospettivo. Questo
approccio fa sì che non vi sia alcuna necessità di un serbatoio inerziale,
poiché il flusso viene regolato in linea”. Oltre al CompactLogix PAC la
macchina dispone di un Allen-Bradley PanelView HMI per l’interazione
con l’operatore, azionamenti a velocità variabile per il controllo delle
pompe Allen-Bradley PowerFlex 525 e 755, una serie di moduli I/O per
l’acquisizione dei dati e l’invio degli input ai
sensori. Implementando un’infrastruttura di
rete basata su Ethernet/IP la macchina può
anche essere controllata da un più ampio si-
stema di controllo di processo. In particolare,
impiegando Ethernet/IP come protocollo di
comunicazione primaria, Corosys può offrire
ai propri clienti un più facile monitoraggio
e manutenzione in remoto nonché, nel con-
tempo, la possibilità di collegare la macchina
alla propria ‘Connected Enterprise’, un ap-
proccio quest’ultimo che i produttori stanno
adottando per trarre vantaggio dall’uso di
macchine, catene di fornitura e clienti inter-
connessi. Esso permette di definire processi
di produzione che sono ricchi di dati/informa-
zioni, che abilitano a una maggiore reattività
alle future esigenze del mercato. Per i pro-
duttori e i loro fornitori, come nel caso di Co-
rosys, un approccio Connected Enterprise, di
fatto, permette di creare un’aziendamaggior-
mente competitiva, innovativa e che in futuro
sarà in grado di fornire spunti per migliorare
la produttività, la sostenibilità e la perfor-
mance finanziaria attraverso l’accelerazione
del time-to-market, la riduzione del costo
totale di proprietà, un migliore utilizzo delle risorse e una gestione più
accorta del rischio d’impresa. Altri vantaggi di un accesso in tempo reale
a informazioni contestualizzate consistono in tempi di downtime ridotti al
minimo, miglioramento della tecnologia e ottimizzazione dei processi, una
maggiore efficienza nell’impiego della forza lavoro e migliore allocazione
delle spese. Il protocollo Ethernet/IP si basa sullo standard Ethernet non
modificato, ciò significa che non vi è molto lavoro da fare per stabilire la
connessione e sono disponibili soluzioni di sicurezza complete anche per
il controllo degli utenti e per impedire accessi ingiustificati.
Manutenzione e diagnostica a distanza
“Adesso, con a bordo i prodotti Allen-Bradley, possiamo offrire diverse
opzioni ai nostri clienti” ribadisce Feider. “Abbiamo registrato benefici reali
in termini di flessibilità e una riduzione del 50% del tempo di ingegneria,
da quattro giorni a solamente due. Rockwell Automation è anche la solu-
zione di controllo di processo standard negli
Stati Uniti e in generale nelle Americhe e il
team di Rockwell Automation in Germania
ci ha dato un sostegno incredibile, soprat-
tutto nella progettazione delle prime unità da
esportare”. Prosegue quindi il responsabile:
“Usiamo PAC CompactLogix standard, che ci
permettono di rendere molto piccoli tutti gli
I/O. Inoltre, utilizzando gli inverter PowerFlex
siamo stati in grado di sfruttare l’ambiente
‘Integrated Architecture’ e ora abbiamo un
software standardizzato che funziona attra-
verso il PAC, gli azionamenti e l’HMI. Nel
nostro caso, i parametri completi vengono
memorizzati nel PAC, il che rende molto più
facile controllare il processo e programmarlo.
L’integrazione è davvero eccezionale con il
PAC, gli azionamenti e l’HMI ed è molto più
semplice fare aggiustamenti. Utilizzando
Ethernet/IP” egli conclude “siamo anche in
grado di offrire manutenzione e diagnostica
da remoto, un servizio che abbiamo imple-
mentato di recente con un cliente che ha sede
a San Diego. Un altro grande vantaggio della
combinazione Ethernet/IP-CompactLogix è
una più facile integrazione nei siti dei clienti,
indipendentemente dall’hardware esistente”. Feider ha anche voluto
sottolineare i vantaggi rispetto ad altri fornitori di automazione: “L’HMI
di Rockwell Automation è più facile da programmare, poiché possiamo
usare i parametri memorizzati, fare modelli e quindi collegare questi ad
altri blocchi di codice; non vi è alcuna necessità di ristabilire link di pro-
grammazione. Le unità sono completamente integrate e possono essere
impostate nel PAC. È anche più facile da programmare, in quanto è tutto
in logica ladder, che risulta di più facile manutenzione; utilizzando una
soluzione basata su Ethernet, infine, non abbiamo spese extra dovute a
costosi plug di programmazione. Tutto l’hardware è poi certificato per il
mercato americano e non vi è alcuna necessità di effettuare adattamenti
ai differenti requisiti dei vari stati”.
Rockwell Automation
www.rockwellautomation.itCorosys Carbonation System (CCS) controlla
in modo continuo e con elevata precisione il
contenuto di CO
2
della birra e di altre bevande
Il PAC CompactLogix viene utilizzato per calcolare i livelli,
un mix ottimale