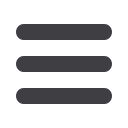
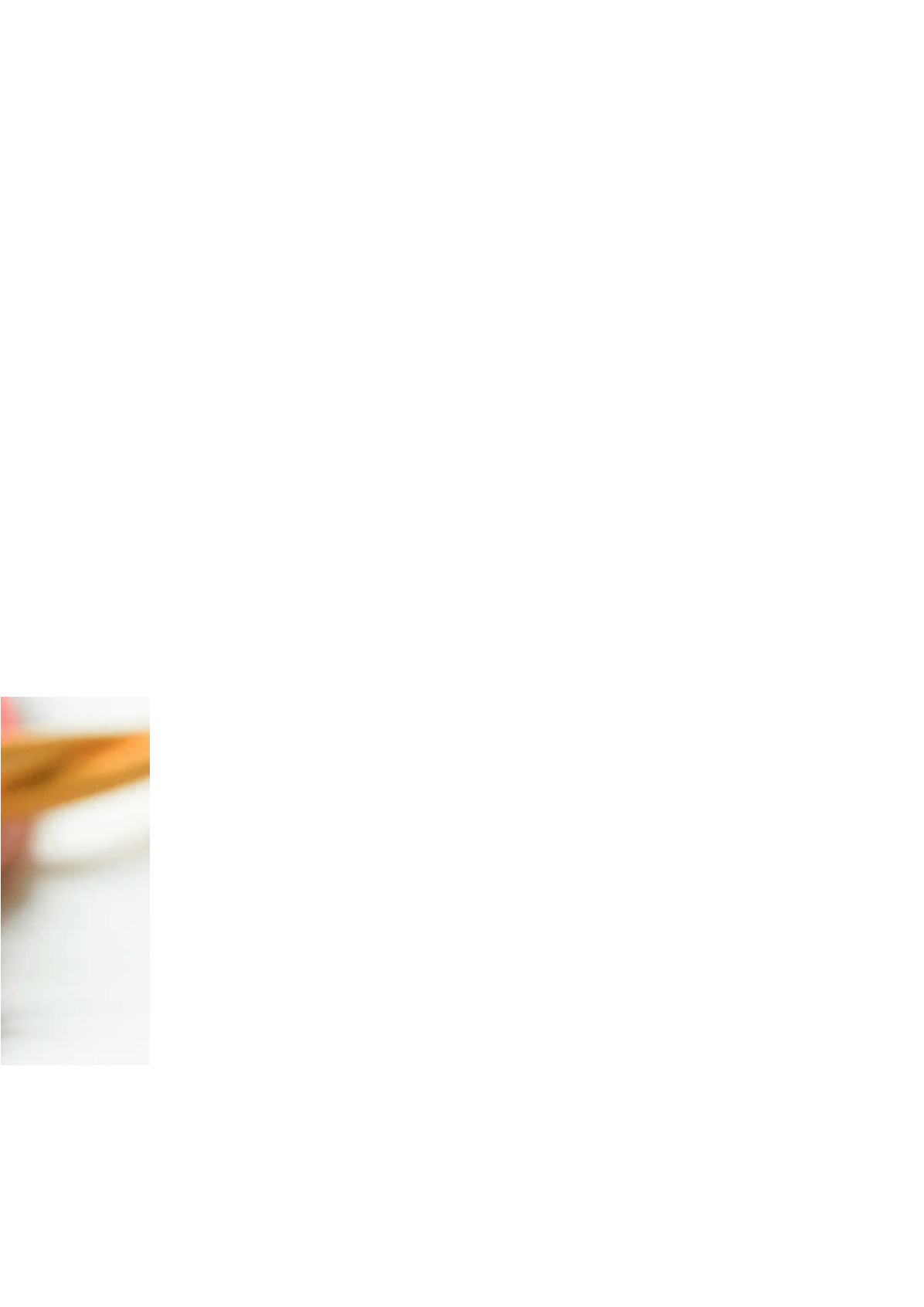
FEBBRAIO 2018
FIELDBUS & NETWORKS
51
tivi e reti sul campo. La trasmissione di dati diagnostici aciclici fornisce
importanti informazioni sullo stato dei dispositivi e della rete, compresa
la visualizzazione della topologia di rete. Il proprietario di un impianto
può utilizzare un’interfaccia HMI per visualizzare graficamente una to-
pologia dell’impianto e una diagnostica granulare. Ciò fornisce al pro-
prietario dell’impianto una rapida panoramica dello stato della rete. La
manutenzione predittiva è di grande interesse per l’industria, in quanto
riduce significativamente i costi. Gli strumenti oggi hanno l’intelligenza
di prevedere quando è necessaria la manutenzione. Tuttavia, sapere che
qualcosa accadrà non è utile a meno che non possa essere comunicato
al sistema di controllo: qui entrano in gioco le soluzioni Ethernet-based
come Profinet. Gli strumenti e i dispositivi di campo hanno la capacità
di comunicare al sistema di controllo che qualcosa non funziona e sup-
portano una manutenzione predittiva completa, includendo il tipo di ma-
nutenzione richiesta (manutenzione necessari, manutenzione richiesta,
allarme di manutenzione)”.
Ethernet e cybersecurity
D.:
Quali impatti ha in termini di sicurezza la sempre più profonda diffu-
sione di Ethernet nell’automazione?
Motta
: “Indiscutibilmente Ethernet introduce aspetti di progettazione
nuovi o scarsamente considerati prima della convergenza delle reti, con
i fieldbus del passato, quali per esempio l’aumento di fatto dei rischi per
la security delle applicazioni industriali. In effetti, oggi il network è uno
solo e questo implica una progettazione olistica, che tenga conto della
security globale, quella della parte enterprise con quella di automazione.
Perché ciò avvenga, un sistema di security deve vedere la luce dalla colla-
borazione integrata di enterprise e automazione, piuttosto che essere svi-
luppata per ‘silos’ indipendenti. La security deve essere parte integrante
dell’attività produttiva di fabbrica e deve includere oltre alla rete, anche i
sistemi di controllo (tenuto conto che quelli ‘legacy’ andranno aggiornati),
le macchine e gli impianti, arrivando a coinvolgere le singole persone, le
prassi e le procedure aziendali nel loro complesso.
Per rispondere alla domanda sempre crescente e in
costante evoluzione di security anche a livello indu-
striale e aiutare i clienti a collegare in modo sicuro
le tecnologie informatiche e quelle di produzione in
tutta l’azienda, Rockwell Automation collabora da
anni con Cisco, azienda che opera a livello mondiale
nel campo del networking e della security”.
Griffini
: “La maggiore diffusione di Ethernet nell’au-
tomazione non comporterebbe di per sé particolari
problematiche di cybersecurity. Queste però stanno
diventando un tema rilevante nell’industria in virtù del
sempre maggiore livello di interconnessione tra reti
di fabbrica (OT-Operations Technology), reti d’ufficio
(IT) e mondo esterno (Internet). Questa interconnes-
sione è favorita dall’impiego di Ethernet, che è alla
base delle soluzioni utilizzate in campo IT e risulta
indispensabile per rendere concreti i vantaggi offerti
da IIoT (Industrial Internet of Things) e Industria 4.0.
Diventa quindi fondamentale per gli operatori di au-
tomazione maturare un’adeguata consapevolezza
dei rischi che corrono adottando soluzioni in grado di garantire un’idonea
protezione. A tal proposito, sta diffondendosi con molta rapidità l’impiego
del protocollo OPC UA, anch’esso a base Ethernet, per collegare livello OT
e IT, garantendo una maggiore protezione dei dati che vengono criptati”.
Candian
: “Soprattutto a causa della crescente messa in rete di connes-
sioni Ethernet fino al livello di campo, occorre considerare alcuni problemi
di sicurezza. Se una comunicazione ‘aperta’ permette di semplificare l’in-
terconnessione dei sistemi di produzione e, quindi, apre nuove interes-
santi opportunità, d’altro canto altrettanto grossi sono i rischi che devono
essere identificati per aggirare i potenziali danni. Un aspetto significa-
tivo da considerare risiede nella valutazione dei rischi relativi ai diversi
sistemi. Se infatti un attacco all’infrastruttura IT colpisce l’integrità dei
dati e, nel peggiore dei casi, si traduce in una perdita di dati aziendali, un
attacco hacker ai processi e all’ambiente di automazione può mettere in
pericolo le persone, danneggiare le capacità di produzione e l’ambiente.
E non è sufficiente implementare un sistema di accesso semplicemente
protetto da password, dal momento che gli attacchi dall’esterno possono
avvenire a diversi livelli. Per una protezione completa degli impianti indu-
striali è stata sviluppata la strategia definita ‘defense in depth’, con cui si
intende un concetto multistrato per gli utilizzatori industriali che protegge
contro gli attacchi sia dall’esterno sia dall’interno, a livello degli impianti
industriali. Il concetto si basa su componenti di sicurezza degli impianti,
sicurezza delle reti e integrità del sistema secondo le norme ISA99 e
IEC62443, che rappresentano gli standard più importanti per la sicurezza
per il settore dell’automazione industriale. La tradizionale protezione di
un impianto garantisce l’inacessibilità fisica, ma la protezione della rete
e dell’integrità del sistema vanno oltre, prevenendo attacchi informatici e
l’accesso da parte di operatori non autorizzati. In questo modo, un poten-
ziale hacker dovrebbe superare molteplici meccanismi di sicurezza a vari
livelli. I requisiti di sicurezza dei singoli strati devono quindi essere presi
in considerazione a livello di impianto”.
Formazione e training
D.:
Il passaggio a soluzioni Ethernet-based e l’impatto su operatori/ma-
nutentori/processisti: quale trade-off tra maggiori funzionalità ed ‘entry
barrier’?
Motta:
“L’adozione di una tecnologia Ethernet, come per esempio Ether-
net/IP, è un percorso innovativo (anche, e soprattutto, formativo) che
dovrebbe andare oltre il mero collegamento di nodi su un fieldbus qualun-
que, come avveniva per le tecnologie passate, e che abbraccia emodifica
anche i processi organizzativi e operativi di un end user. Sarà essenziale,
per esempio, che le tecnologie di una linea produttiva siano in futuro il più
possibile agevolmente fruibili anche dagli operatori IT sulla stessa rete.
‘La rete’: ecco la chiave di tutto. Essa dovrà aiutare a identificare, racco-
gliere, interpretare e condividere inmodo sicuro i dati utili, con le persone
che ne possono usufruire, nel contesto giusto per prendere le decisioni
appropriate a livello di gestione della produzione. In effetti, la possibilità
di accedere facilmente al patrimonio di informazioni disponibili oggi sulla
rete sta guidando sempre più gli utilizzatori a fare quel salto di qualità che
consentirà loro di passare dal mero collegamento di semplici nodi remoti,
all’integrazione degli stessi, per fruire della maggiore disponibilità di dati
senza che questo introduca nuove problematiche, ma diventi un valore
aggiunto accessibile a manutentori e operatori”.
Candian
: “Per i produttori di macchine e impianti, l’utilizzo di reti Ethernet
based, come Profinet, riduce al minimo i costi di installazione, proget-
tazione e messa in servizio. Il proprietario dell’impianto beneficia della
facilità di espansione, della disponibilità elevata dell’impianto e dell’auto-
mazione rapida ed efficiente. Il personale addetto allamanutenzione è ora
potenziato come non mai, iniziando la giornata guardando la schermata
di manutenzione dell’HMI può determinare: quali dispositivi, se presenti,
richiedono attenzione immediata; quali dispositivi possono essere esa-
minati in un secondo momento; quali strumenti devono essere esami-
nati periodicamente per determinare il tempo di manutenzione ottimali.
I tempi di manutenzione saranno quindi suddivisi tra queste tre attività,
con il solo problema occasionale di un’emergenza reattiva. Inoltre, quando
devono indagare su uno strumento, il primo passo non richiede alcuno
spostamento: si collegano semplicemente allo strumento attraverso la
rete e fanno in modo che lo strumento comunichi loro il problema e, pos-
sibilmente, anche la possibile soluzione”.
Fonte: www.pixabay.com