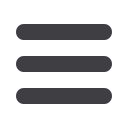
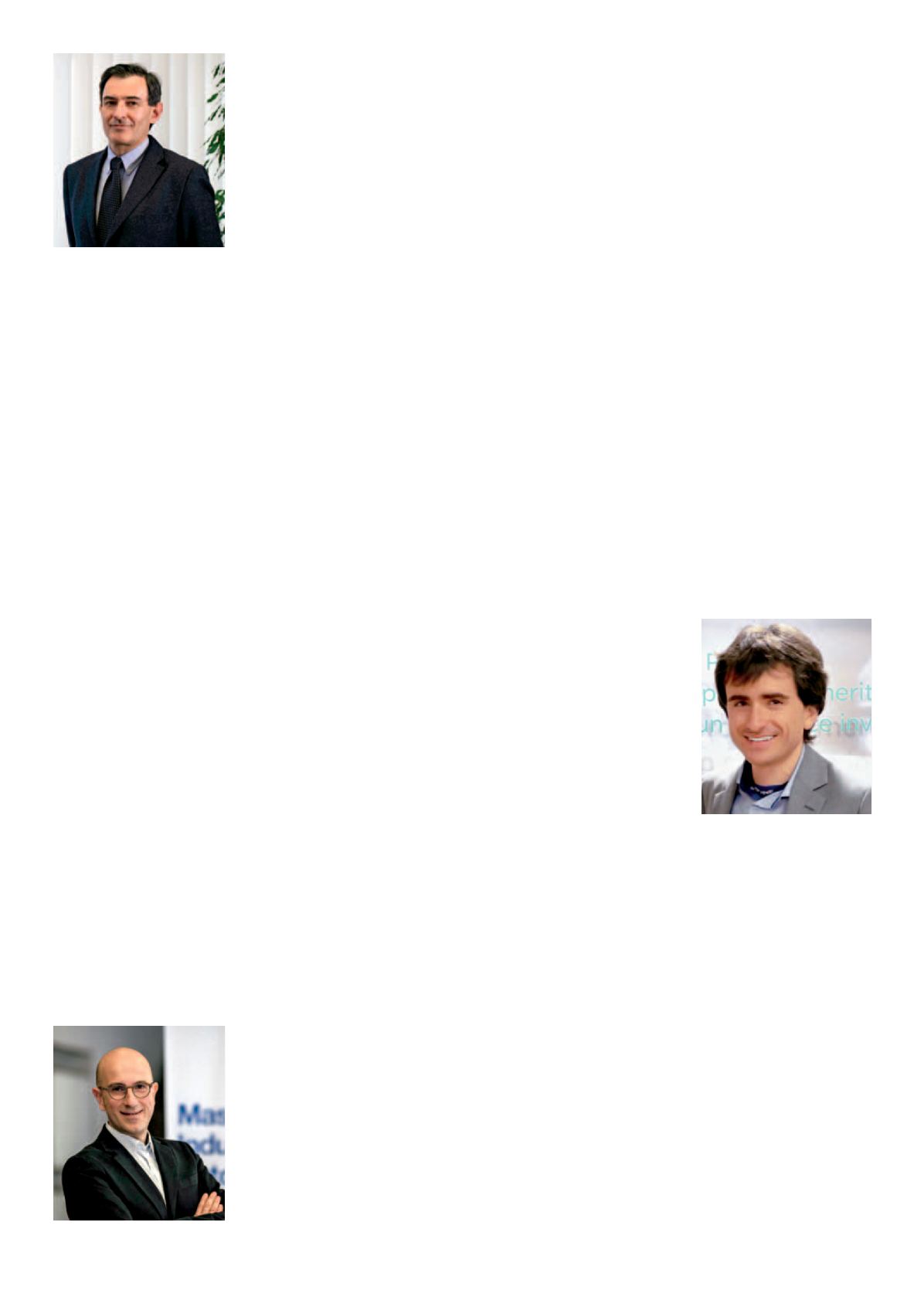
NOVEMBRE 2017
FIELDBUS & NETWORKS
71
logy) e OT (Operations Technology)
convergano su una singola tecnologia
condivisa. Nuove figure professionali
devono contribuire a diffondere questa
tecnologia, soddisfacendo i requisiti di
una connettività diffusa. Connettività
che sta diventando una richiesta irri-
nunciabile per la stragrande maggio-
ranza delle applicazioni industriali: la
possibilità di connetterle direttamente
sulla rete dello stabilimento degli
utilizzatori impone di padroneggiare
sempre più le tecniche di configura-
zione delle reti TCP/IP. Innanzitutto, si tratta di sviluppare conoscenze
che permettano ai progettisti di automazione di creare reti industriali
connesse, senza soluzione di continuità, alle reti IT, per abilitare l’accesso
ai dati operativi dove questi siano effettivamente richiesti e da parte degli
operatori che ne necessitano. Oggi, la stragrande maggioranza dei dispo-
sitivi industriali in uso nelle nuove installazioni produttive sono abilitati
all’IP con un approccio più o meno standard a seconda dei protocolli di
automazione usati, ma un numero sempre maggiore di dispositivi IP con
standard aperti di derivazione non industriali si stanno rapidamente af-
fermando anche nelle aree produttive. Questi dispositivi, come i tablet,
le videocamere e i lettori Rfid, aprono la strada a nuove possibilità per
aumentare la connettività e la collaborazione fra OT e IT. Per chiarire quali
siano nel concreto le richieste in termini di networking di Industria 4.0, si
può cliccare sullo spotlight ‘fare Industria 4.0’ presente sul sito web di
Rockwell Automation”.
Alberto Griffini
, product manager Advanced PLC&Scada di
Mitsubishi
Electric
( it3a.mitsubishielectric.com ): “Le competenze richieste riguar-
dano un campo sempre più ampio: dal sensore intelligente al sistema
IT attraverso tutti i livelli della smart factory, la comunicazione tramite
rete è il fattore abilitante dell’azienda 4.0. L’integrazione tra elementi del
sistema fabbrica, a partire dai dispositivi di campo, ai sistemi di visualizza-
zione e controllo, all’archiviazione ed elaborazione dati, sino alla pianifica-
zione della produzione legata agli ordini clienti, alle scorte di magazzino e
alle forniture esterne, corre su un filo conduttore costituito da reti di scam-
bio dati. In tale contesto, la capacità di offrire soluzioni inter-operanti con
prodotti e sistemi di costruttori differenti rappresenta un valore aggiunto.
Mitsubishi Electric ha perciò avviato da più di dieci anni il programma
denominato e-F@ctory Alliance, una partnership tra oltre 3.000 aziende
in grado di fornire soluzioni a livello di campo, di controllo, di processo e
di business, tutte interoperabili e accomunate dall’adozione di un unico
protocollo standard, che permette al cliente finale di disporre di una solu-
zione davvero completa”.
Ezio Fregnan
, HR Training Manager di
Comau
( www.comau.com/IT ):
“Innanzitutto occorre un’expertise consolidata: Comau vanta un know-
how maturato nel tempo, che le con-
sente di comprendere al meglio tutte
le dinamiche e le potenzialità offerte
alle aziende dalla ‘digital revolution’,
per guidarle con successo nel pro-
cesso di innovazione che caratterizza
l’Industria 4.0. Altro asset importante
è la presenza di un approccio globale
al mercato: Comau opera attraverso
una struttura internazionale e con il
supporto di una rete di collaborazioni
strategiche, avviate in tutto il mondo,
con importanti atenei, istituti di ricerca, aziende internazionali e start-up.
Questa modalità operativa le ha permesso di ampliare e diversificare
costantemente le proprie competenze, per poter sviluppare soluzioni di
automazione sempre più innovative e al passo con le nuove esigenze del
mercato. A queste risorse si aggiunge una visione innovativa, capace di
anticipare i trend del futuro. Da tempo infatti Comau è impegnata nel
rendere concreta una nuova era dell’automazione, aperta, connessa, sem-
plice da comprendere e da utilizzare, grazie allo sviluppo di prodotti e tec-
nologie all’avanguardia, a un nuovo concetto di fabbrica, che ha chiamato
‘Humanufacturing’. Con questa espressione, Comau definisce la sua ‘via
all’Industria 4.0’, per rispondere alle sfide e alle esigenze di un mercato
in continua evoluzione. La fabbrica 4.0, diventa un sistema di produzione
integrato e connesso, caratterizzato dalla collaborazione sinergica e in
totale sicurezza tra l’uomo, che ricopre un ruolo centrale all’interno del
processo produttivo, e le macchine industriali, grazie all’impiego di robot
collaborativi e delle nuove tecnologie digitali”.
Fieldbus&Networks:
Quali competenze occorrono per superare le dif-
ficoltà d’intesa, di linguaggio, di ‘ottica’ fra i due ‘mondi’ IT e OT, che in
azienda devono cooperare?
Marco Gamba
, project manager Smart Manufacturing di
Schnei-
der Electric
( www.schneider-electric.it ): “Il punto di partenza, che
non si insegna facilmente con percorsi di formazione o aggiorna-
mento, è la capacità di collaborare: senza questa disponibilità non è
possibile realizzare il necessario incontro fra i mondi dell’IT e dell’OT.
Per chi viene dal mondo dell’Information Technology, l’obiettivo è
imparare a conoscere i processi industriali gestiti dalle tecnologie
operative, capire le necessità di chi
si occupa di produzione e arrivare
a parlare ‘la stessa lingua’. Il per-
sonale e il management operativo,
d’altro canto, dovranno imparare a
confrontarsi apertamente e con fidu-
cia con i colleghi IT, così da sfruttare
le loro competenze per raccogliere
e gestire, prima di tutto, l’enorme
mole di dati che si generano quando
si introducono applicazioni in ottica
di Industria 4.0. Si tratta di ribaltare
la tradizionale percezione che si ha
dell’IT come di qualcosa che ‘cala
dall’alto’ sul livello operativo, ingenerando il timore che l’informatica
si sostituisca alle capacità di controllo della produzione interne, ma-
gari delocalizzando in un cloud non più residente nello stabilimento le
funzionalità chiave. In realtà, esiste una soluzione differente, basata
su una visione che anche Schneider Electric ha adottato. Si tratta di
sfruttare la potenza e flessibilità del cloud come risorsa fondamentale
per il monitoraggio di un impianto non in tempo reale, per l’analisi
dei trend di consumo energetico, per ottenere report di produzione,
aggregare dati provenienti da impianti produttivi diversi, per abilitare
servizi digitali innovativi, quali la manutenzione predittiva ‘as-a-ser-
vice’. Tutto questo si può fare mantenendo il controllo in tempo reale
dell’impianto all’interno dello stabilimento, in ottica di edge control,
affidandolo alle persone che vi operano”.
Mario Borali
, amministratore delegato e direttore tecnico di
Au-
toma
( www.automa.it ): “La connessione in rete, dal punto di vista
teorico, non è problematica. Le reti però devono essere opportuna-
mente segmentate e dotate di tutti gli elementi di sicurezza attiva
necessari. Ma la predisposizione della rete è solo la premessa in-
Roberto Motta di Rockwell
Automation
Ezio Fregnan di Comau
Marco Gamba di Schneider
Electric