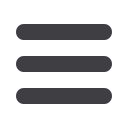
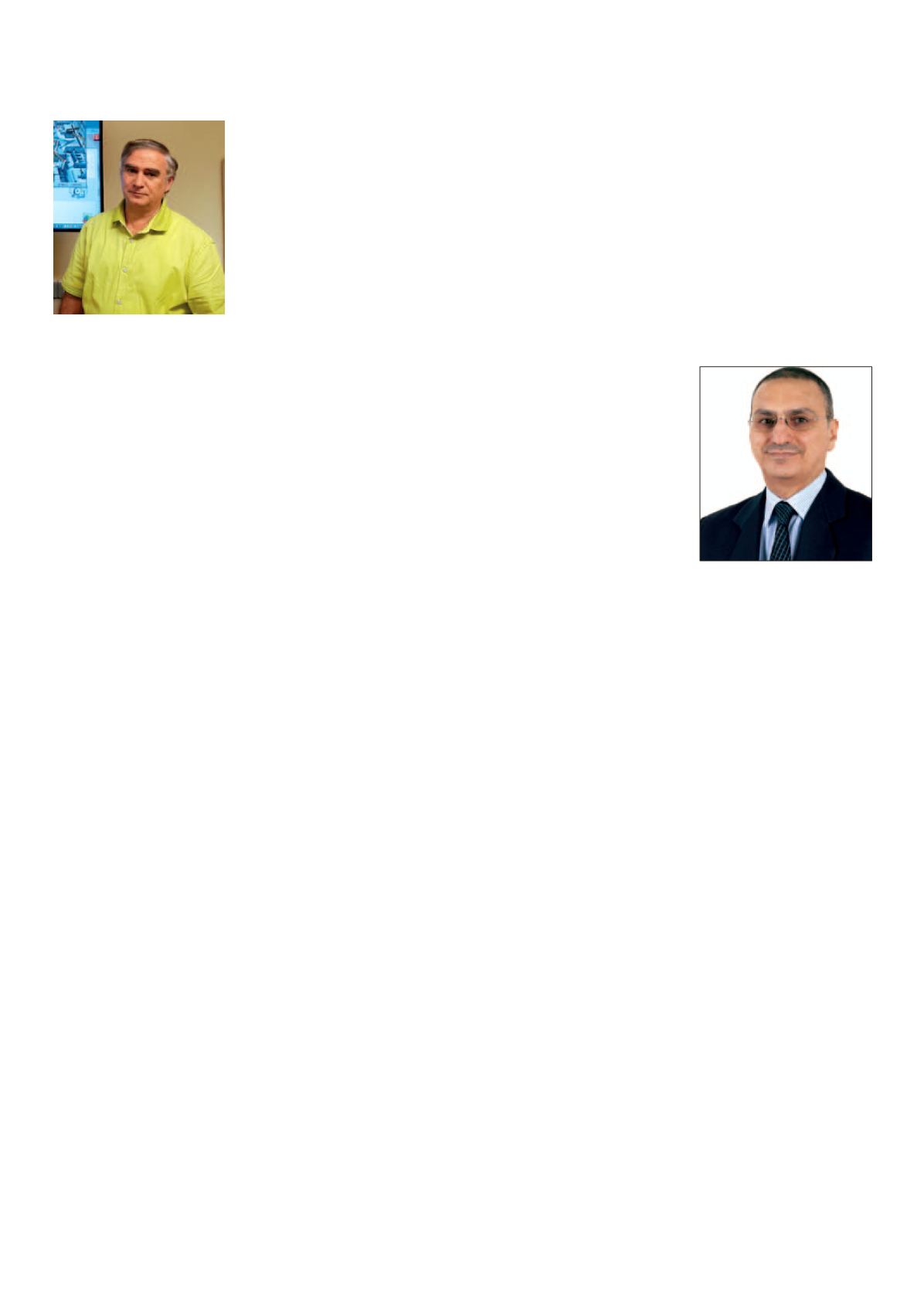
NOVEMBRE 2017
FIELDBUS & NETWORKS
72
Fieldbus & Networks
dispensabile per avere dei sistemi
interconnessi. La vera difficoltà
è l’integrazione, anche perché i
‘mondi’ IT e OT sono a loro volta
stratificati in diversi livelli. Nei
progetti di integrazione le proble-
matiche sono: connessione, sincro-
nizzazione di mondi che viaggiano
a velocità diverse, strutturazione
dati. La rete risolve una parte es-
senziale della problematica della
connessione; per la sincronizza-
zione e strutturazione dei dati occorre definire correttamente flussi,
funzionalità e responsabilità di ciascuno dei livelli, o moduli, coin-
volti nell’integrazione”.
Motta:
“La digitalizzazione è un processo innovativo che va oltre i meri
prodotti e le soluzioni e che abbraccia e modifica anche i processi or-
ganizzativi e operativi e la formazione culturale di tutto il personale in
un’azienda. Riteniamo che sarà essenziale, per esempio, che le tecno-
logie di una linea produttiva siano in futuro il più possibile agevolmente
fruibili anche dagli operatori IT. Esse dovranno aiutare a identificare,
raccogliere, interpretare e condividere in modo sicuro i dati ‘utili’, con
le persone che ne possono ‘usufruire’, nel contesto ‘giusto’ per prendere
le decisioni ‘appropriate’ a livello di gestione della produzione. L’utilizzo
del patrimonio delle informazioni disponibile oggi sta guidando sempre
più le aziende a fare quel salto culturale e di competenze che consen-
tirà di passare dal mero collegamento di semplici utenze operative su
una rete di comunicazione, all’essere aziende intelligenti interconnesse:
solo in questo modo la disponibilità sempre maggiore di dati rappresen-
terà un valore aggiunto anziché introdurre nuove problematiche”.
Candian:
“Le sfide generate da Industry 4.0 e IIoT impongono concetti
innovativi e prodotti efficienti che da soli però non bastano, vitali sono
anche personale specializzato e competenze specifiche. Nell’ambiente
industriale le interruzioni della rete spesso richiedono soluzioni veloci e
semplici. Qui ogni minuto perso si trasforma in perdite produttive ed econo-
miche. Spesso semplicemente non è possibile aspettare il supporto IT per
la risoluzione dei problemi in campo. È perciò essenziale per il personale
d’impianto OT sapere come modificare o installare i componenti quando
richiesto. In tutti i più disparati ambiti industriali, si pensi alle acciaierie, a
impianti petrolchimici, linee di produzione automobilistiche o nel settore
food&beverage, i componenti della rete devono essere in grado di soppor-
tare condizioni ambientali diverse e spesso estreme. La sfida fondamentale
durante la pianificazione e l’implementazione delle reti industriali si fonda
sulla chiara comprensione delle esigenze dei clienti e dei flussi di lavoro
critici del mondo OT. Non è possibile implementare una rete sicura, al-
tamente disponibile e flessibile, utilizzando una soluzione standard office
IT. Le sequenze operative e i possibili fattori d’interferenza devono essere
conosciuti proprio partendo dal linguaggio e dalle esigenze specifiche del
mondo OT. La connessione del mondo OT al sistema IT aziendale richiede
di conseguenza un elevato livello di esperienza e competenza del sistema
di automazione e un confronto con i responsabili IT per una condivisione
delle rispettive esigenze, al fine di definire, con un’intesa comune, l’imple-
mentazione di un layer specifico di ‘backbone aggregation’ Industriale per
l’interconnessione dei due ‘mondi’. Per questo Siemens offre una gamma
completa di servizi ed esperti con competenze specifiche, oltre che oppor-
tunità di formazione ai clienti nel settore industriale”.
F&N:
Per integrare al meglio sistemi che impiegano tecnologie diffe-
renti è spesso importante conoscere la ‘storia’ dell’impianto e il fun-
zionamento dei processi di lavorazione, conoscenze che si maturano in
azienda. Non sarebbemeglio investire sull’aggiornamento del personale
interno, piuttosto che su consulenze esterne?
Raffaele Esposito
, product manager Safety I/O&Networking di
Phoe-
nix Contact
( www.phoenixcontact.it ): “Le due possibilità indicate nella
domanda non costituiscono aspetti completamente separati e destinati
per forza a non poter coesistere. La giusta combinazione tra un aggior-
namento del personale interno e il ricorso a consulenza esterna dipende
da caso a caso, ma il propendere per una soluzione può non escludere
completamente l’altra. Un consulente
degno di questo nome, pur non po-
tendo ovviamente essere un esperto
‘tuttologo’, dispone normalmente di
tutte le competenze necessarie per lo
scopo specifico per il quale viene coin-
volto, con esperienze spessomaturate
in anni di attività in un ben preciso set-
tore o su una ben definita tecnologia.
In questo senso, può essere proprio
il consulente esterno a fungere da
‘tutor’ per lo sviluppo delle risorse
interne chiamate a operare insieme a
lui. Questo soprattutto quando le fonti
di formazione istituzionale, ovvero scuole e università, non sono ancora in
grado di rispondere ai fabbisogni di formazione, soprattutto per tecnologie
innovative. Per quel che è la nostra esperienza, la proposta da parte dei
fornitori di tecnologia, soprattutto se innovativa, di corsi di formazione
a completamento dell’offerta di prodotto è prassi abbastanza usuale. E
questo tipo di formazione si rivela di solito estremamente efficace per
consentire alle risorse interne degli utilizzatori di prodotto di acquisire le
opportune conoscenze atte a favorire le giuste competenze specifiche. In
definitiva, assolutamente corretto perseguire lo sviluppo di competenza
delle risorse interne, ma nessuna preclusione a ricorrere a consulenze
esterne per raggiungere tale obiettivo”.
Borali:
“I progetti di integrazione dei sistemi informativi aziendali non
nascono con Industria 4.0, anche se ne sono certamente molto stimolati.
Le conoscenze interne all’azienda sono fondamentali: i progetti di inte-
grazione hanno, come presupposto, la definizione chiara e scritta delle
esigenze aziendali e delle possibili soluzioni. La consulenza esterna può
aiutare moltissimo in questo processo, perché generalmente un esterno
non cade nella trappola del ‘si deve fare così perché è quello che facciamo
da sempre’. Spesso inoltre, le varie funzioni aziendali non hannomai vera-
mente fatto un percorso di definizione e condivisione dei flussi informativi
e vivono quotidianamente le problematiche di processi spesso studiati a
tavolino e imposti da terzi. In ottica Industria 4.0 ogni funzione aziendale,
ogni modulo produttivo, ogni macchina deve smettere di considerarsi un
mondo a sé stante. Tutto si deve trasformare in ‘moduli’ che hanno come
principio di fondo l’interconnessione, ossia la possibilità di mettere a di-
sposizione la propria funzione/capacità per gli interlocutori che necessi-
tano di utilizzarla. Su questi aspetti la formazione interna è essenziale”.
Gamba:
“Per ottenere macchine e processi industriali più efficienti
sfruttando la connettività è necessario, ovviamente, conoscere lo storico
dell’impianto, per avere un termine di paragone. L’ideale sarebbe fare
Raffaele Esposito di Phoenix
Contact
Mario Borali di Automa