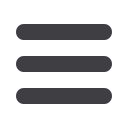
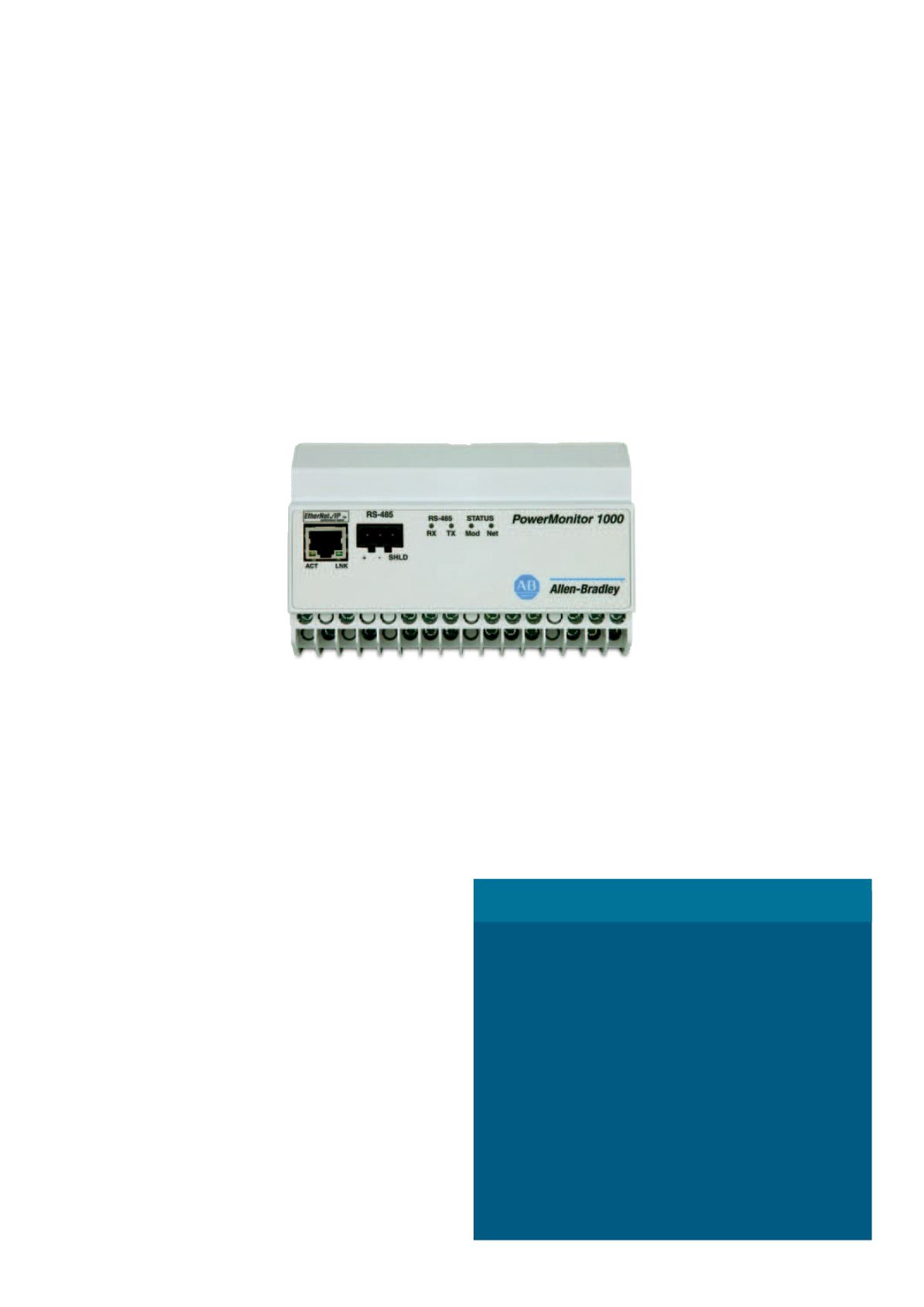
Brialdi. “Relativamente alle attività che svolgiamo in questi mercati,
Rockwell Automation rappresenta per noi una garanzia: vuoi per qua-
lità e prestazioni delle sue soluzioni di automazione, vuoi per l’ampia
accettazione che queste trovano nel continente americano, vuoi infine
per l’ampia disponibilità che il suo personale riesce sempre a garan-
tirci relativamente a supporto e assistenza tecnica in loco”.
100 km di …energia
Appena 100 km di fiume. Non un grande corso d’acqua dunque, ma
una risorsa disponibile per garantire una media produzione energe-
tica in maniera sostenibile. L’obiettivo del cliente di GEA Orengine
era sfruttare il DMV del fiume andando a installare, in parallelo alla
valvola di dissipazione dell’energia rilasciata dal deflusso di acqua
nel tratto di fiume a valle della diga, una turbina idraulica capace
di convertire in energia elettrica questa quota parte di energia (2,5
MW), che altrimenti sarebbe andata sprecata.
Per rispondere al meglio alle specifiche del cliente, GEA Orengine
desiderava offrire la possibilità di associare al controllo tradizionale
un approccio più innovativo e in linea con gli obiettivi di ottimizza-
zione, sostenibilità e riduzione dei
costi. Un’unica architettura integrata
avrebbe permesso di controllare il si-
stema, oltre a fornire piena visibilità
non solo sui dati relativi al consumo
di energia, ma anche sulle vibrazioni
della macchina, e di implementare un
efficace programma di manutenzione
predittiva basata sulle condizioni.
Rockwell Automation ha raccolto que-
sta sfida e ha risposto alle esigenze
di GEA Orengine con un approccio in-
novativo, proponendo una soluzione
unica, completa e integrata che, oltre
alla gestione e controllo della turbina
elettrica, permettesse al cliente finale
di ridurre i costi di esercizio. A tal fine, è stata proposta una singola ar-
chitettura integrata con funzionalità di analisi e controllo dei consumi
energetici che, oltre ad aver ulteriormente elevato il livello di soste-
nibilità del progetto, ha contribuito a ridurre i costi operativi dell’im-
pianto. Allo stesso modo, la possibilità di monitorare le vibrazioni ha
permesso di implementare un piano di manutenzione predittiva, che
ha ridotto il rischio di guasti e fermi imprevisti e, di conseguenza, i
costi a essi collegati. L’architettura si basa sulla capacità di calcolo di
quattro controllori Allen-Bradley CompactLogix (PAC) interconnessi in
rete Ethernet/IP, che utilizzano anche il protocollo di trasmissione IEC
60870-5-104 che, in ambito di automazione di centrali elettriche, co-
stituisce lo standard di riferimento per quanto riguarda le funzionalità
di telecontrollo. I quattro CompactLogix, inoltre, sono stati interfac-
ciati con il controllo centrale dell’impianto, anch’esso equipaggiato
con unità Rockwell Automation più potenti, questa volta di tipo Allen-
Bradley ControlLogix (PAC). Al fine di raggiungere le migliori presta-
zioni, nonché l’immunità dalle interferenze elettromagnetiche (EMI),
quale supporto fisico di trasmissione è stata scelta la fibra ottica. Per
il monitoraggio e la protezione del generatore, ovvero per il controllo
del carico energetico e dei parametri a esso correlati, è stato instal-
lato un Allen-Bradley PowerMonitor 1000, che è stato interfacciato
ai PAC Rockwell Automation attraverso protocollo Ethernet/IP. Infine,
per l’analisi delle vibrazioni è stato utilizzato un modulo di misura-
zione dinamica standard della serie Allen-Bradley XM, una soluzione
di controllo generale online che Rockwell Automation ha espressa-
mente ideato per il monitoraggio dell’albero, della carcassa o delle vi-
brazioni del basamento nell’installazione di macchine rotanti. A esso
è stato collegato in maniera dedicata un Panel PC Industriale Versa
View 6181P standard, sul quale è stata installata la suite software
Rockwell Automation Emonitor Condition Monitoring, per implemen-
tare un efficace programma di manutenzione predittiva basato sulle
condizioni. Si tenga presente che gli impianti di generazione dell’e-
nergia si trovano in una caverna, raggiungibile attraverso una stretta
galleria, dove le gravose condizioni ambientali non devono costituire
un ostacolo alla continuità di esercizio.
Installazione senza ‘intoppi’
Come spiega Brialdi, oltre alle caratteristiche di affidabilità e perfor-
mance, la decisione di utilizzare un’architettura mono fornitore è stata
motivata anche dalla completa disponibilità da parte di Rockwell Au-
tomation di tutti i moduli necessari, incluso quello per il monitoraggio
delle vibrazioni. Cosa non da poco, poiché ha permesso di realizzare un
ambiente completamente integrato senza dover ricorrere a interfacce
di comunicazione o di conversione dati. “Sfruttando un’infrastruttura
già esistente e grazie alla tecnologia Rockwell Automation siamo
stati in grado di realizzare un progetto
100% sostenibile e altamente replica-
bile in qualsiasi impianto idroelettrico,
che ha permesso di aumentarne la ca-
pacità di 2,5 MW e di fornire energia
sufficiente al fabbisogno di un intero
paese” afferma Brialdi. “Sebbene
l’applicazione fosse caratterizzata da
una certa complessità d’impianto,
non vi sono stati particolari intoppi.
Anzi. Grazie alle funzionalità offerte
dall’ambiente di programmazione
RSLogix 5000 le fasi di sviluppo e
messa a punto del software, avvenute
in loco, hanno richiesto appena tre
settimane di lavoro, con un notevole
contenimento dei costi totali. Questo, grazie anche al supporto offerto
dal team tecnico di Rockwell Automation che” prosegue Brialdi “spe-
cialmente per quanto riguarda la parte di analisi delle vibrazioni, ci ha
dato una mano determinante in termini di competenze applicative”.
Rockwell Automation -
www.rockwellautomation.it@
< % [ \ ]^^^ _
% & `[ "
j + x %
La soluzione Rockwell Automation installata include:
– 4 controllori Allen-Bradley CompactLogix
– 3 HMI Allen-Bradley PanelView Plus
– 1 Panel PC industriale Versa View 6181P
– 1 PowerMonitor Allen-Bradley
– Moduli Allen-Bradley della serie XM
– Software Emonitor
I risultati conseguiti:
– Controllo e monitoraggio delle vibrazioni su
un’unica piattaforma senza necessità di conversione
di protocolli
– Aumento di 2,5 MW di potenza erogata
– Sfruttamento del DMV e sviluppo di un progetto ad
alta sostenibilità
@; #${@| $;j } ;&j;~j
NOVEMBRE 2017
FIELDBUS & NETWORKS
49